[gallery size=full columns=1]
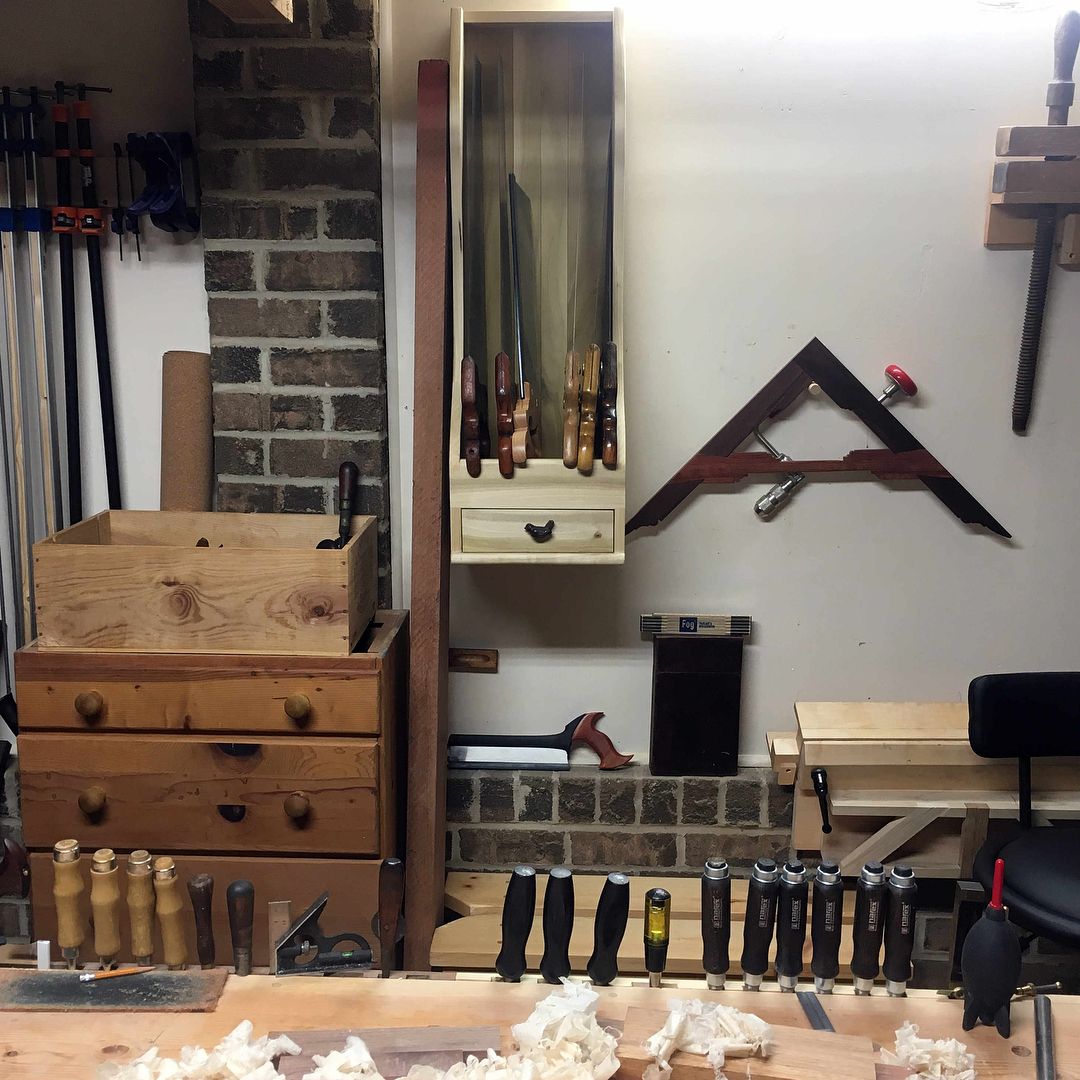
[gallery size=full columns=1]
Here’s an example of a really cheap scrub plane. I made it with a $5 old hybrid I picked up from an antique store. The hardest part of this was grinding the iron into a concave shape using a (you guessed it) grinder. I had some trouble getting mine evenly ground, but it worked great after I sharpened it up on my stone. I did have to widen the hole in the bottom up so it didn’t get all clogged up.
Here’s a pic of it in use on a slab of maple.
Here’s the iron after I ground it with a grinder and sharpened it up on a stone.
And here’s the mouth I opened up with a chisel so shavings don’t get stuck.
One of these days, I’m going to pick up a weightier plane for a few bucks to make another one with more mass.
Here’s a small project to replace a handle on a Chinese-style ladle. The handle I had to replace was a cheap bit of pine pushed in to the metal part of the ladle. Instead of trying to replicate that, I decided to make a handle that would house the ladle. So I grabbed a scrap of walnut, cut it down to size with my rip saw, and then scratched my head for a while figuring out how to secure it.
My solution was to first drill the hole that would house the ladle. I locked it in my vise and used a brace I recently picked up for a few bucks to drill the hole. I also got an auger file recently and had just sharpened up some bits I had also picked up at the local flea market … so I was eager to try it out. It worked surprisingly well.
Then I took a length of 3/4" oak dowel and used a spokeshave to shave it down a bit so I could mount the new handle on the face of my workbench to work on it. I shaped the handle with spokeshave, chisels, and a file.
This is the handle in rough form mounted on a dowel. I used a chisel to slim it down.
Then I worked on it with the spokeshave.
I tapered it with the spokeshave, then smoothed out the rough edges with a file and chamfered the edges with a chisel. I finished it off with some flexible sand paper.
And here it is attached the to ladle.
I recently completed a new vise Moxon benchtop vise. The hardware and a good portion of the design inspiration is from Tools for Working Wood. It’s hard maple, 23" between the screws, cork lined, and finished with Danish oil. It was made with hand tools only, as part of my online apprenticeship with the Hand Tool School.
The holes in the front and back jaw were easy to drill, but the right side was just a tad off when I put the screws in and tested the alignment and it was causing it to stick. So the second shot is a dowel with sandpaper I used to open up the rear jaw hole just a bit so there was no rubbing or sticking on the wood.
Here are the mortises on the underside of the vise that house the nuts. These were chopped out, of course, with mortise chisels.
Since I didn’t own a rabbet plane when I made this, I used a saw to cut the top and bottom rabbets. This took forever. I had to a lot of clean up work with the router plane to them square.
I made a 45 degree guide for the cut, but it was only really useful to eyeball things to ensure I was at the same angle all the way across. Since I wanted a lip at the top of the front jaw, I couldn’t cut all the way to the angle guide in the back and it was too much of a hassle to get the guide at the right height in back to match up with cut I was making. So I really just relied on cutting down to the top and bottom lines marking the angle on the front jaw. Then I just planed it down. I figured I didn’t really care if it was exactly 45 degrees, anyways…as long as it was uniform and about 45 degrees, I was good. The angle is there so there’s room to angle saw cuts without cutting into the vise wood.
Front:
Side: (the cork is to keep the vice jaws from damaging wood)
Back: (the top piece is so that there’s a flat surface for dovetail joinery)